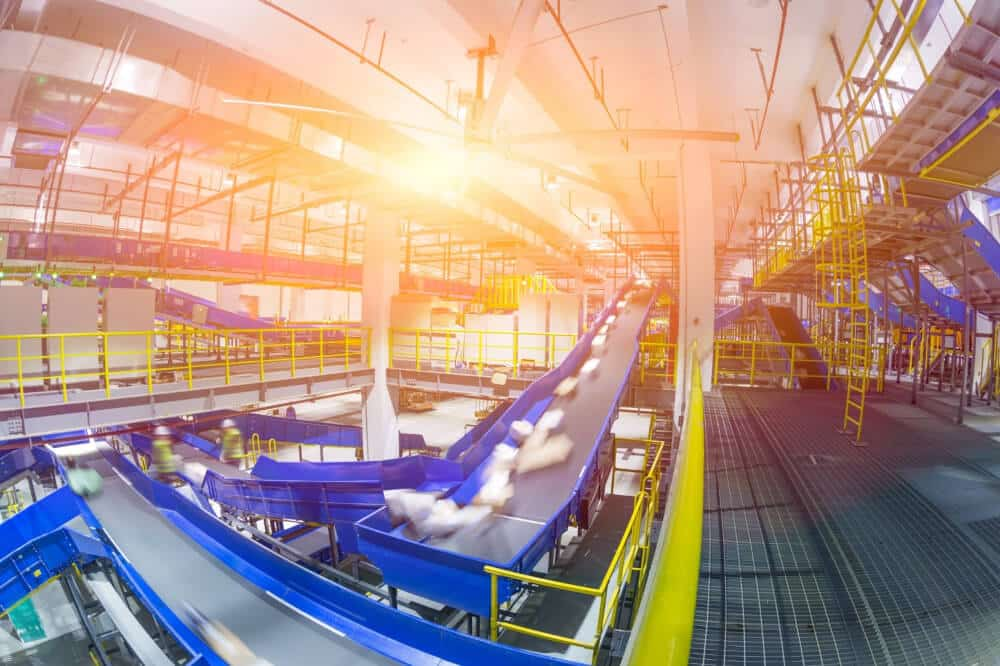
The landscape of modern warehousing has undergone a remarkable transformation since the first conveyor belt systems revolutionized material handling operations decades ago. What began as a simple innovation has evolved into sophisticated automated systems that form the critical infrastructure of today’s high-performing warehouses. In an era where efficiency is currency, automated conveyor systems have emerged as the backbone of warehouse automation, enabling facilities to meet ever-increasing demands while overcoming persistent challenges.
As we examine the transformative potential of automated conveyor systems in warehousing, one thing becomes clear: facilities that leverage this technology effectively gain significant advantages in operational efficiency, cost management, and ability to scale with demand. The following sections will demonstrate how the right conveyor solutions, properly implemented, can become your warehouse’s most valuable productivity asset.
The Current State of Warehouse Automation
Today’s warehouse operators face mounting pressures: labor shortages that show no signs of abating, supply chain disruptions that demand greater operational resilience, and consumer expectations for faster fulfillment than ever before. Some of the most common challenges include:
#1 Labor Shortages
The warehousing industry continues to grapple with a persistent labor shortage. Facilities are operating with fewer workers than optimal levels, creating significant operational bottlenecks. This workforce gap is compounded by high turnover rates.
#2 Supply Chain Disruptions
Global supply chain volatility has become the new normal. Warehouses must now operate with greater flexibility and resilience to manage unpredictable inventory flows, fluctuating lead times, and sudden demand spikes.
#3 Increasing Consumer Demands
The “Amazon effect” has reset the standard for fulfillment speed, with same-day and next-day delivery having become the expectation rather than the exception. This pressure for faster throughput places enormous strain on traditional warehouse operations.
What Does This Mean for Warehouses?
These converging challenges present both significant obstacles and strategic opportunities for today’s warehouse operators. The labor shortage forces facilities to accomplish more with fewer workers, making automation not just a productivity enhancement but an operational necessity.
Supply chain disruptions demand greater system flexibility and redundancy—warehouses must quickly adapt to changing inventory patterns and unpredictable demand spikes without sacrificing efficiency. Meanwhile, accelerating consumer delivery expectations compress fulfillment timelines, requiring warehouses to process orders with unprecedented speed and accuracy.
The Evolution of Warehouse Operations
The shift from manual to automated processes typically progresses from essential mechanization (simple conveyor systems) through semi-automation (barcode scanning, zone routing) to advanced automation (sophisticated conveyor networks with sortation) and finally to intelligent automation with IoT sensors and AI-driven analytics.
Throughout this evolution, conveyor systems have emerged as the critical foundation that ties warehouse functions together. They serve as the central nervous system of warehouse automation, enabling seamless movement between zones, integration with complementary technologies, workflow smoothing through accumulation capabilities, and precision product positioning for accurate order fulfillment.
Understanding Automated Conveyor Systems
Automated conveyor systems represent the cornerstone of modern warehouse automation, offering far more functionality than their predecessors. These sophisticated systems serve as the foundation for efficient material flow and enable the integration of advanced technologies throughout the facility.
Types of Automated Conveyor Systems
Today’s warehouse operations can leverage several distinct conveyor technologies, each optimized for specific applications:
- Belt Conveyors: Versatile systems ideal for transporting a wide variety of products ranging from small items to large packages
- Modular Belt Conveyors: Flexible systems allowing for curves, inclines, and declines while maintaining product stability
- Flexible Chain Conveyors: Space-optimizing systems that can navigate multiple planes with tight turns
Key Technological Advancements
Modern automated conveyor systems have evolved significantly, incorporating innovations that enhance performance and flexibility:
- Precision Controls: Modern motor and drive systems enable precise speed control, soft starts/stops, and variable speeds
- Modular Design: Quick-connect components and standardized interfaces allow for rapid reconfiguration
- Smart Sensors: Embedded photoelectric and proximity sensors enable real-time tracking and system responsiveness
- Energy Efficiency: Low-friction materials and zone control systems reduce power consumption
- Reduced Maintenance: Self-lubricating components and predictive maintenance capabilities minimize downtime
Dorner’s Conveyor Product Lines with Specific Applications
Dorner offers a comprehensive range of conveyor solutions designed for specific warehouse applications:
1100 Series Miniature Conveyors
Applications:
- Small part transfers in tight spaces
- Medical and pharmaceutical sorting
- Electronics component handling
- Integration into OEM equipment
- Inspection and quality control stations
Key Features: Ultra-compact 3/4″ frame height, clean room certified (Class 100), backlit capability for inspection, and pinch drive design for consistent performance
2200 Series Low-Profile Conveyors
Applications:
- Space-constrained picking stations
- Multi-level transport systems
- Light assembly operations
- E-commerce order fulfillment
- Product transfers between processes
Key Features: Low-profile design (as little as 1.85″ height), available in widths from 1.75″ to 24″, configurable for curves and inclines, and load capacity up to 150 lbs
2700 Series Medium Duty Conveyors
Applications:
- E-commerce order processing
- Packaging line product transfers
- Automotive parts handling
- Machine integration in manufacturing
- Robotic pick-and-place operations
Key Features: Width options from 8″ to 36″, load capacity up to 150 lbs, speeds up to 400 ft/min, and versatile design for growing operations
3200 Series Heavy-Duty Conveyors
Applications:
- Main line conveying in distribution centers
- Heavy parts transport in manufacturing
- High-speed sortation operations
- Bulk product handling
- Integration with scanning and vision systems
Key Features: Width options up to 48″, load capacity up to 1,000 lbs, speeds up to 600 ft/min, and configurable for straight, curved, or inclined paths
DCMove Series Conveyors
Applications:
- High-volume straight-run transport
- Parcel handling in distribution centers
- Cross-docking operations
- E-commerce order sortation
- General material transport in warehouses
Key Features: Economical painted steel frame, widths up to 60″, lengths up to 98′, and internally mounted motor for reduced footprint
FlexMove Flexible Chain Conveyors
Applications:
- Complex routing through space-constrained areas
- Elevation changes between warehouse levels
- Navigating around fixed infrastructure
- Product accumulation and buffering
- Creating efficient workflows in irregular spaces
Key Features: Ability to make tight turns and elevation changes, multiple chain options (friction, cleated, conductive), and modular design for easy reconfiguration
AquaGard & AquaPruf Sanitary Conveyors
Applications:
- Food product handling and packaging
- Pharmaceutical processing
- Medical device manufacturing
- Any environment requiring sanitary standards
- Facilities subject to wash-down procedures
Key Features: Stainless steel construction, tool-less disassembly in under 2 minutes, compliance with BISSC, NSF, and FDA regulations, and rounded frame members for easy cleaning
Precision Move Conveyors
Applications:
- Automated quality inspection
- Robotic pick-and-place integration
- Precise assembly operations
- Controlled indexing applications
- Machine vision systems integration
Key Features: Positioning accuracy within ±0.02″, available in both 2200 and 3200 Series platforms, and servo motor options for controlled acceleration/deceleration
Pallet System Conveyors
Applications:
- Precise product positioning and routing
- Assembly line automation
- Electronic and medical device manufacturing
- Cleanroom applications
- Robotic integration
Key Features: Multiple technologies, including timing belt (DualMove), edge roller (ERT series), flexible chain options, positioning accuracy up to ±0.5mm, and customizable pallet designs
Integration Capabilities
The true value of modern conveyor systems extends beyond simple transport to serve as integration platforms for complementary technologies. Advanced warehouse automation relies on this seamless connectivity between physical conveying and digital control systems.
Dorner’s sophisticated conveyor solutions feature integration points for vision systems, barcode scanners, RFID readers, and robotic pick-and-place equipment. This connectivity enables real-time tracking, automated sortation, and dynamic routing based on warehouse management system instructions.
By selecting the appropriate conveyor technology for each warehouse area and ensuring seamless integration between systems, operators can create a unified automation solution that maximizes throughput, accuracy, and operational efficiency while maintaining the flexibility to adapt to changing requirements.
Strategic Applications in Warehouse Operations
Automated conveyor systems are more than simple transport mechanisms in today’s warehouses; they are strategic assets that can transform operational capabilities when deployed thoughtfully. By understanding how these systems can be applied to specific warehouse functions, operators can maximize productivity gains and return on investment.
Material Handling and Product Flow Optimization
The foundation of warehouse efficiency begins with streamlined product movement throughout the facility. Implementing a well-designed conveyor network creates predictable, consistent flow paths that minimize manual handling and accelerate throughput.
Dorner’s 3200 Series conveyors excel in mainline applications, creating efficient highways for product movement with speeds up to 600 ft/min. The 2200 Series offers a low-profile solution for facilities with space constraints that can be configured for overhead transport, maximizing usable floor space while maintaining smooth product flow.
For complex layouts requiring products to navigate around existing infrastructure, Dorner’s FlexMove system offers unmatched routing flexibility with capabilities for tight turns, inclines, and declines within a single continuous system.
Order Fulfillment and Picking Processes
E-commerce growth has dramatically increased the importance of efficient order fulfillment. Automated conveyor systems enhance picking operations by delivering products to pickers (goods-to-person) or transporting totes between picking zones.
The compact design of Dorner’s 2200 Series makes it ideal for integration with picking stations, while accumulation capabilities allow for buffering during variable picking rates. For high-precision applications requiring exact product positioning for robotic picking, Precision Move conveyors provide repeatable positioning within ±0.02″.
Sortation and Diverting Capabilities
Effective sortation is crucial for accurate order fulfillment and efficient inventory management. Modern conveyor systems employ sophisticated diverting mechanisms to route products to their appropriate destinations automatically.
Dorner’s 3200 Series with Activated Roller Belt™ (ARB) technology enables precise lateral transfers for sortation applications without complex mechanical diverters. For warehouse operations requiring a comprehensive sortation solution, Dorner’s integrated systems can incorporate pop-up transfers, pushers, and gate diverters to create versatile, reconfigurable sortation networks.
Accumulation and Merging Operations
Balancing production flow in warehouses often requires accumulation zones to buffer products during downstream slowdowns or to prepare for merging operations. Advanced conveyor systems provide controlled accumulation that prevents product damage while maintaining throughput.
The FlexMove conveyor system offers efficient product accumulation with its low-pressure design, allowing products to accumulate gently without excess back pressure. For heavier items, Dorner’s 3200 Series with zero-pressure accumulation modules provides reliable buffering while protecting product integrity.
Merging operations benefit from Dorner’s side-acting merge modules and precision controls that synchronize product flow from multiple lines into a single stream without collisions or jams.
Future-Proofing Your Warehouse
In today’s rapidly evolving logistics landscape, implementing conveyor automation is not just about solving current challenges but also preparing for future growth and technological advancement. A forward-thinking approach to warehouse automation ensures that today’s investments continue to deliver value as operations expand and new technologies emerge.
Scalability Considerations for Growing Operations
Planning for growth requires modular system architecture that allows for straightforward extensions without significant rework. Dorner’s conveyor systems are engineered with this modularity, enabling sections to be added or reconfigured as operational needs evolve, typically with additional capacity beyond current needs to accommodate near-term growth.
Adaptability to Changing Product Lines
As product offerings evolve, conveyor systems must adapt accordingly with features like adjustable guide rails, reprogrammable sorting logic, and convertible workstations. Selecting systems like Dorner’s 2200 Series with straightforward belt replacement options enables quick adaptation when product characteristics change.
Warehouses handling diverse product lines find particular value in flexible systems like FlexMove, which can be reconfigured with minimal downtime. This adaptability allows operations to pivot quickly as market demands shift, protecting the automation investment even as product lines evolve.
Integration with Emerging Technologies
The next generation of warehouse automation will leverage AI, machine learning, and advanced robotics, requiring conveyor systems with open architecture controls and standardized communication protocols. Physical integration points for cameras, sensors, and robotic interfaces throughout the conveyor network support future technological adoption without significant modifications.
Dorner’s Precision Move and Pallet System conveyors are particularly well-suited for these emerging technologies due to their precise positioning capabilities and standardized control interfaces. Their documented API interfaces enable connection with AI and machine learning platforms that will drive future optimization.
Data Collection and Analytics Capabilities
Modern conveyor systems serve as valuable data sources when equipped with throughput counters, barcode scanners, and condition monitoring sensors. This sensor network enables real-time visualization of key metrics and supports predictive maintenance approaches that can reduce downtime compared to reactive models.
Warehouses leveraging these data capabilities have identified optimization opportunities delivering additional efficiency gains beyond their initial automation benefits. Dorner’s control systems support comprehensive data collection for integration with analytics platforms, enabling continuous improvement through data-driven decision-making.
Preparing for Industry 4.0 Advancements
The convergence of physical and digital systems—Industry 4.0—represents the future of warehouse operations, characterized by IoT connectivity and intelligent conveyor networks that continuously communicate their status. This connectivity enables decentralized intelligence where conveyor systems make local decisions based on current conditions rather than centralized commands.
Dorner’s advanced control options position their conveyor systems as ready components for Industry 4.0 implementation, with ongoing development ensuring compatibility with emerging warehouse automation standards. The warehouses that will thrive in the coming decade will establish flexible, data-driven conveyor foundations today that can adapt to tomorrow’s technological and market changes.
Implementing automated conveyor systems represents a pivotal investment in warehouse productivity and operational excellence. Throughout this guide, we’ve explored how these systems address critical challenges facing today’s warehouse operators while delivering measurable performance improvements. The benefits of strategic conveyor automation are substantial and multifaceted, from labor efficiency and throughput gains to space optimization and error reduction.
Dorner’s comprehensive range of conveyor solutions—from the compact 1100 Series to the heavy-duty 3200 Series, versatile FlexMove system, and specialized AquaPruf platforms—provides the foundation for customized automation that addresses your specific operational challenges. With over 50 years of conveyor innovation experience, Dorner’s application engineers can help you identify the optimal automation approach for your facility’s unique requirements.
In an era of labor constraints, supply chain volatility, and increasing customer expectations, automated conveyor systems offer more than operational improvements—they provide a sustainable competitive advantage. The warehouses that thrive in the coming decade will leverage intelligent automation to achieve levels of efficiency, accuracy, and adaptability that simply aren’t possible with traditional manual operations. By partnering with Dorner to implement strategic conveyor automation today, you position your warehouse operations for immediate productivity gains and long-term market leadership.