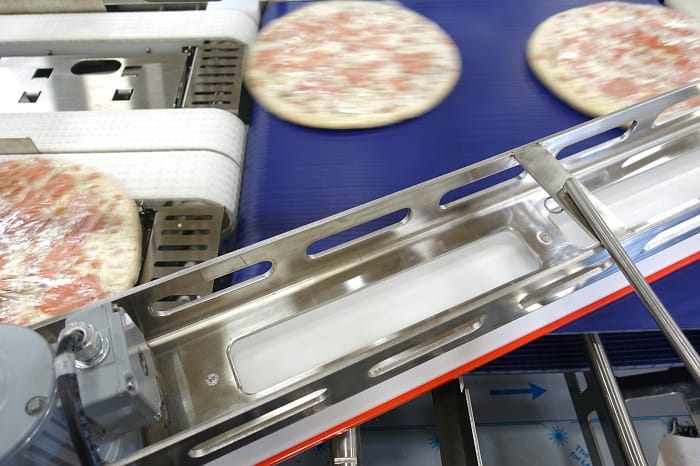
When a customer needed to upgrade their existing food processing line to merge two lanes of frozen pizzas into a single lane, Dorner’s Engineered Solutions Group designed the perfect custom solution.
Dorner’s Engineered Solutions Group (ESG) gives extra attention to building conveyor systems with unique dimensions and performance characteristics above and beyond Dorner’s regular conveyor platforms.
ESG is a full-service team comprised of drafters, designers, project managers, electrical and mechanical engineers working together to evaluate your application and design a custom conveyor system that meets your efficiency goals and objectives.
ESG offers services in concept, design and needs analysis, along with layout and 2D or 3D modeling. Its services include mechanical design, phased engineering, controls (HMI, PLC and servo panel builds), factory and site acceptance testing, as well as replacement and spare-parts recommendations for bench stock.
Conveyor systems have become highly automated, integral components of a processing or packaging line. The key to their success is properly orientating product on the conveyor and positioning it correctly for the next step in the processing/packaging line.
Orientation is done through a variety of techniques, such as controlling the flow and speed of product both upstream and downstream of the conveyor system; using accessories such as photo eyes and servo drives for very precise product movement; or using devices such as diverters, pushers, lane guiding and gates.
Dorner Engineered Solutions are ideal for applications involving:
- Merging, diverting, rotating and sorting products
- Increasing efficiency; reducing product loss and downtime, and maximizing throughput
- Accumulation systems
- Depositing and rejects
- Indexing and positioning
- Inspection, testing and sortation
- Product handling including multiple sizes and shapes
These are all great examples of the types of custom conveyor systems Dorner’s Engineered Solutions Group can design, build and install – just like they did for the pizza manufacturer.
In that application, pizzas enter the merge system from an inline nitrogen freezer at a rate of 75 per minute. Then, they need to be merged into one lane to be wrapped for shipment. ESG devised a system where, before the merge, the pizzas move down two conveyors equipped with sensors to stop movement at precise times.
This product stop, often lasting less than a second, ensures that the two lanes can merge seamlessly. This custom conveyor solution uses photoelectric sensors, pneumatic cylinders with flow controls, dynamic guide and a PLC to fully control the orientation of pizzas as they prepare to be wrapped.
Overall the system is only 10 feet long, which gave the customer a compact, space-saving design that increased their pizza output.
With years of experience in providing engineering expertise to customers across numerous industries, Dorner’s Engineered Solutions Group is able to draw from a vast base of conveyor solutions knowledge and apply it to your specific custom conveyor needs.
Learn more about Dorner’s Custom Systems and the type of solutions we can provide for you.